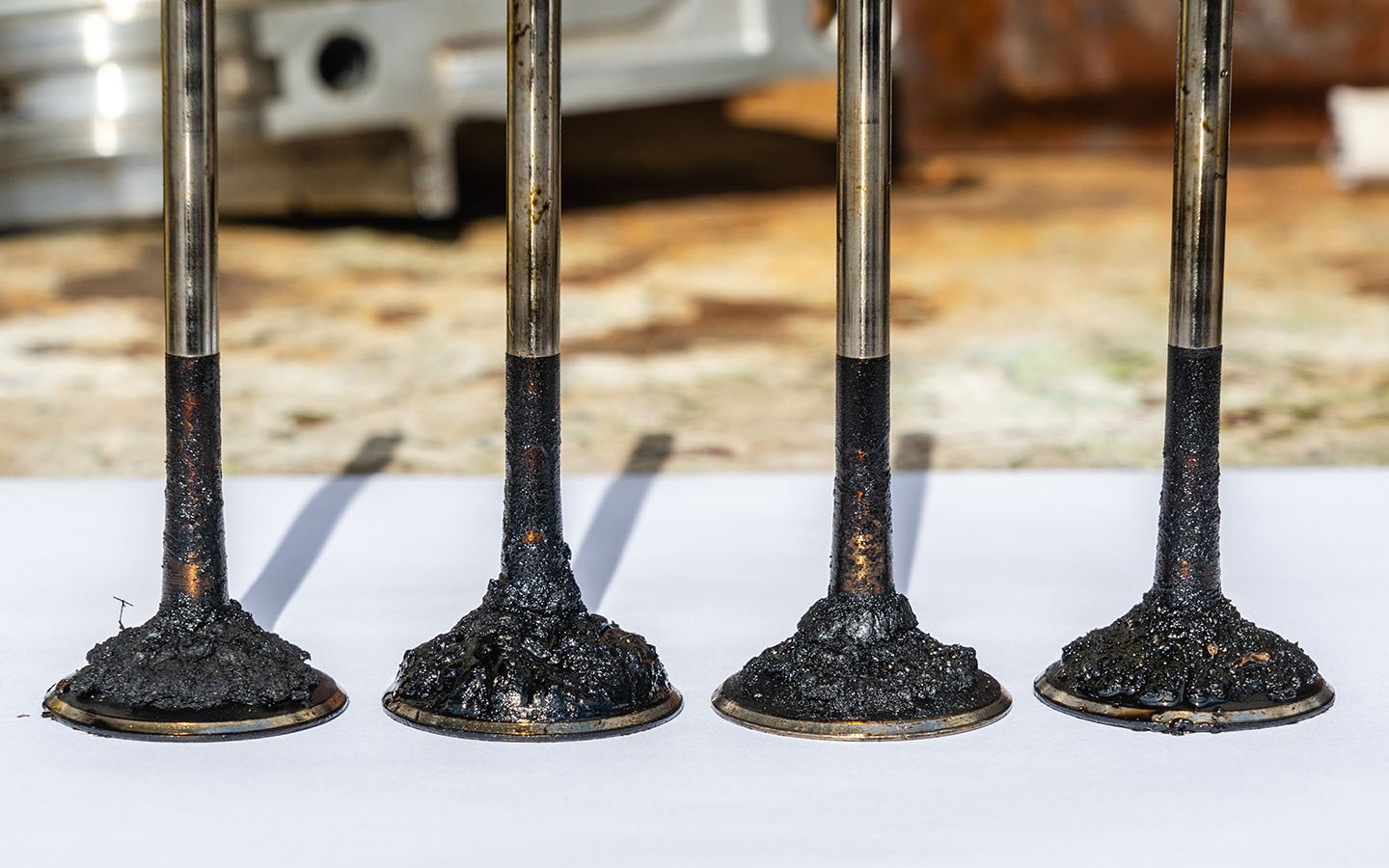
One of the largest manufacturers
of engine valve
Follow Us On:
Home > Engine Valve Manufacturing: A Comprehensive Guide
When it comes to manufacturing engine valves, attention to detail is paramount. Every aspect, from material selection to quality control, plays a crucial role in ensuring optimal performance and longevity. In this guide, we'll explore how to manufacture engine valves while considering key factors that contribute to their quality and reliability.
Begin by carefully choosing the material for your engine valves. Consider factors such as strength, heat resistance, and corrosion resistance. Stainless steel, titanium, and inconel are popular choices for their exceptional properties. Selecting the right material sets the foundation for a durable and high-performing valve.
Once you've chosen the material, precision machining is essential to shape the valve to exact specifications. Utilize CNC machining technology to achieve accuracy and consistency throughout the manufacturing process. From forging to finishing, precise machining ensures that each valve meets the required dimensions and tolerances.
Enhance the mechanical properties of your valves through proper heat treatment. Processes like quenching and tempering improve hardness, toughness, and wear resistance. Tailor the heat treatment regime to suit the specific requirements of your engine application, ensuring that the valves can withstand the demands of operation.
Apply surface coatings to enhance the durability and performance of your valves. Coatings such as nitriding, chrome plating, or ceramic coatings provide protection against corrosion, abrasion, and high-temperature oxidation. Choose coatings based on the operating conditions and performance goals of your engine.
Maintain rigorous quality control throughout the manufacturing process. Implement non-destructive testing methods like ultrasonic testing and visual inspections to detect any defects or deviations from specifications. By ensuring strict quality standards, you can deliver valves that meet industry requirements and exceed customer expectations.
Conduct thorough performance testing to validate the quality and functionality of your valves. Evaluate factors such as flow characteristics, sealing integrity, and fatigue strength. Use the insights gained from testing to fine-tune your manufacturing processes and continuously improve the performance of your valves.
Engine valves are integral components of internal combustion engines in passenger cars, trucks, and high-performance vehicles. They regulate the flow of air and fuel into the combustion chamber and contribute to engine efficiency and power.
Marine engines rely on high-quality valves to ensure reliable operation in demanding marine environments. Valves play a crucial role in regulating the flow of air and fuel in marine propulsion systems, contributing to efficient and powerful engine performance.
Gas and steam turbines used in power generation facilities require precision-engineered valves to control the flow of steam and gases. High-performance valves ensure efficient energy conversion and reliable operation of power generation plants.
Locomotive engines depend on robust valves to deliver power and traction for trains. Engine valves play a vital role in controlling the combustion process and optimizing fuel efficiency in locomotive propulsion systems.
Valves used in oil and gas extraction, refining, and processing operations must withstand high pressures, temperatures, and corrosive environments. Engine valves manufactured with durability and reliability in mind are essential for the smooth operation of oil and gas facilities.
Aerospace engines demand high-performance valves for aircraft propulsion systems and rocket engines. Engine valves designed for aerospace applications must meet stringent quality and reliability standards to ensure safe and efficient operation in extreme conditions.
Conduct thorough performance testing to validate the quality and functionality of your valves. Evaluate factors such as flow characteristics, sealing integrity, and fatigue strength. Use the insights gained from testing to fine-tune your manufacturing processes and continuously improve the performance of your valves.
Category​
Recent Posts​
SIMPLIFY THE QUALITY, DETERMINE THE PRODUCT